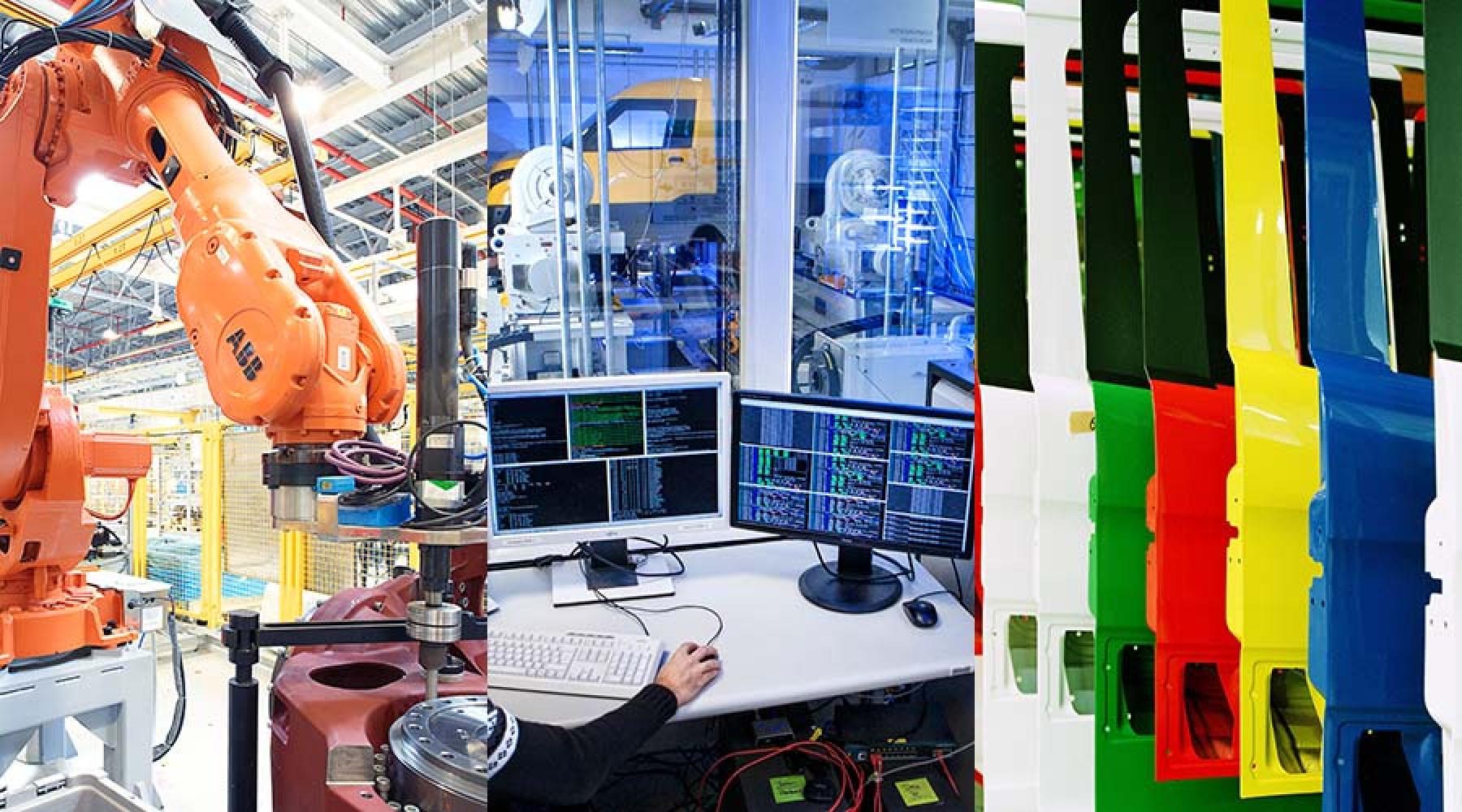
Foto: Tacton Systems / www.siemens.com/presse / Scania
Industrie 4.0: Svensk industri satsar på framtidsteknik
2015-04-08
Tillverkningsindustrin står inför stora utmaningar, bland annat går utvecklingen mot ökad efterfrågan på individualiserade och kundanpassade produkter. I Tyskland har politikerna och näringslivet gått samman om Industrie 4.0 i syfte att åstadkomma en effektiv och flexibel produktion genom ökad digitalisering. Men även i Sverige pågår ett intensivt arbete för att utveckla smarta fabriker med uppkopplade maskiner och självstyrande produktion.
Bilar som Volvo, Volkswagen, BMW och Audi tillverkas numera i massor med olika varianter. Det stora urvalet av karosser, motorer, växellådor, lackeringar, fälgar, klädslar, stolar och så vidare gör att dagens bilköpare har miljontals eller rentav miljarder av olika kombinationer att välja mellan. Därtill kommer specifika särkrav på olika marknader.
Men bilindustrin är inte den enda bransch som går mot en ökad kundanpassning av sitt sortiment. En liknande utveckling är på gång inom de flesta områden samtidigt som kunderna kräver samma korta leveranstider och låga pris som gäller för massproducerade produkter – en ekvation som bara går att lösa genom en satsning på nya tekniska lösningar.
– De ökade kraven på individualisering i kombination med hårdare kostnadspress gör att industrin nu står inför ett teknikskifte. Genom att flytta ut intelligens och handlingskraft från centrala datorer ända ut till enskilda maskiner och produkter får man produktionssystem som kan agera självständigt, men ändå är säkra för människor i produktionen, säger Johan Stahre, professor och avdelningschef för produktionssystem på Chalmers Tekniska Högskola i Göteborg.
Tillgänglig teknik används på nya sätt
Det är inte första gången som industrin står inför vad som allmänt betecknas som ett paradigmskifte. Ända sedan industrialismens vagga stod för flera hundra år sedan har industrin genomgått stora omvandlingar i takt med introduktionen av ny teknik som i sin tur gett upphov till nya banbrytande lösningar. I slutet av 1700-talet och början av 1800-talet kom ångmaskinerna, i början av 1900-talet elektriciteten och under 1970-talet datorerna som gjorde det möjligt att automatisera delar av tillverkningen.
Den fjärde stora industriella revolutionen handlar nu om näringslivets svar på ”the internet of things” – ”sakernas internet” – med smarta, självorganiserande fabriker, där maskinerna är uppkopplade och produkterna ”taggade” med så mycket information att de själva styr produktionen.
I Tyskland har regeringen under ledning av förbundskansler Angela Merkel lagt fast framtidsprojektet Industrie 4.0 i samarbete med näringslivet. Det yttersta målet är att den tyska tillverkningsindustrin genom en massiv satsning på ny teknik ska kunna bibehålla sin ledarposition och stärka sin konkurrenskraft gentemot lågkostnadsländer som erbjuder billig produktion.
Men även runt om i världen pågår liknande satsningar. I USA har flera företag, organisationer och universitet gått samman i Smart Manufacturing Leadership Coalition (SMLC) och General Electric har tagit initiativ till ett konsortium - Industrial Internet Consortium – tillsammans med ATT, Cisco, IBM, Intel och Siemens med inriktning på industriellt internet. Sydkorea och Schweiz är andra länder som satsar hårt på att utveckla sin tillverkningsindustri med hjälp av senaste teknik.
– Produktionsinnovationer handlar inte alltid om ny teknik, utan om att använda tillgänglig teknik på nya sätt. Henry Ford kom heller inte med några revolutionerande lösningar. Däremot kombinerade han på ett smart sätt ett antal befintliga tekniker för att skapa det löpande bandet och massproduktionen, konstaterar Johan Stahre.
Hållbar produktion främjas genom innovationsprogram
Även i Sverige pågår flera omfattande program med inriktning på produktionsutveckling. Ett exempel är Produktion2030, som startade 2013 och som är ett strategiskt innovationsprogram för hållbar produktion som koordineras av Teknikföretagen.
– Målet är att Sverige 2030 ska vara ett av världens främsta länder för hållbar produktion, förklarar Cecilia Warrol, som är programchef för Produktion2030.
Programmet har sin utgångspunkt i den agenda – Made in Sweden 2030 – som togs fram i nära samarbete mellan Teknikföretagen, Svenska Produktionsakademien, industriforskningsinstitutet Swerea IVF, Chalmers, KTH och IF Metall för ett par år sedan. Agendan handlar om de långsiktiga insatser som krävs för att stärka innovation samt utveckling och produktion av varor och tjänster.
Produktion2030 finansieras av innovationsmyndigheten Vinnova och kommer de närmaste två åren att genomföra två utlysningar per år för olika projekt. För närvarande är drygt 10 forsknings- och innovationsprojekt på gång och målet är att kunna finansiera ytterligare 10 – 15 projekt. Programmet har även initierat en ny nationell forskarskola inom produktion och planerar även flera aktiviteter för att involvera små och medelstora företag i forskningsprojekten.
– Bland Teknikföretagens medlemsföretag finns en stor potential att identifiera produktionsrelaterade utmaningar och utveckla nya lösningar, säger Cecilia Warrol, som också konstaterar att Sverige saknar den koordinering och struktur av insatserna som Tyskland har med sitt Industrie 4.0.
– Ändå har den svenska modellen en styrka genom att vi är förändringsbenägna, trendkänsliga och har god förmåga att åstadkomma informella samarbeten. Samtidigt är det anmärkningsvärt att Sverige som it-nation, med världsledande företag som till exempel Ericsson, saknar politisk plattform för de här frågorna, menar Cecilia Warrol.
Tysk-svenskt forskningsutbyte
Inom det strategiska forskningsområdet produktion startade 2009 även två andra nationella satsningar i Sverige – dels Sustainable Production Initiative, som är ett samarbete mellan Chalmers, Lunds universitet, flera stora industriföretag samt Fraunhofer-centret i Göteborg, dels framtidslabbet XPRES, Excellence in Production Research, på KTH i Stockholm.
XPRES drivs i samarbete med Mälardalens högskola (MDH) samt Swerea IVF och har till syfte att utveckla en plattform för produktionsforskning och att hitta nya, smarta produktionslösningar.
Arbetet sker i nära samarbete med företag som Scania, Volvo CE, Sandvik, ABB och försvarskoncernen Saab. Men även utländska institutioner som till exempel tyska Fraunhofer-Institut är involverade i verksamheten.
– Sverige har många framstående företag med avancerad tillverkning av produkter och komponenter. Trots vår blygsamma storlek är vi till exempel ett av fem länder i världen med tillverkning av stridsflygplan. Den stora utmaningen ligger i att arbeta för att bibehålla vår starka ställning som industrination, understryker Thomas Lundholm, teknologie doktor och chef för XPRES.
Det är framförallt tre områden som står i fokus på XPRES – tillverkning med nya material och processer, produktframtagning med hänsyn till ett livscykelperspektiv samt anpassningsbar och flexibel produktionsteknik, det vill säga en produktion som är snabbt omställningsbar och anpassad för produktion av individualiserade produkter.
– I alla områden ingår digitala tillämpningar eller, som vi valt att kalla det, Sim Factory efter dataspelet Sim City. Framtidsvisionen är en virtuell fabrik som är helt integrerad med den fysiska. I den virtuella fabriken görs alla tester och on-simuleringar innan den fysiska fabriken är klar för driftsättning, säger Thomas Lundholm.
Standardiserade lösningar utarbetas
XPRES har hittills genomfört flera projekt i samarbete med fordonsindustrin inom ramen för det statliga forskningsprogrammet Fordonsstrategisk Forskning och Innovation, FFI, som leds av Vinnova och Energimyndigheten. Nyligen avslutades det treåriga projektet LISA, Line Information System Architecture, där man utvecklat en ny typ av så kallad referensarkitektur för produktionslinjer inom fordonsindustrin.
– Produktionslinjerna är, enkelt uttryckt, uppbyggda av twittrande maskiner, som är uppkopplade och kommunicerar med varandra genom ett ständigt flöde av tweets, det vill säga små korta meddelanden som kan användas för att styra produktionen, förklarar Thomas Lundholm.
Tekniken för att skapa smarta fabriker med intelligenta maskiner och självstyrande produktion börjar nu komma på bred front. Men däremot är det inte alla företag som vare sig har kompetens eller ekonomiska resurser att bygga upp en helt ny maskinpark med intelligenta maskiner. En av de stora utmaningarna är därför att hitta enkla, standardiserade kommunikationslösningar som fungerar för de flesta typer av utrustning.
– Det är mot den bakgrunden vi nu står i begrepp att starta ett nytt projekt, LISA 2. Fokus ligger på att utveckla enkla applikationer, fullt jämförbara med apparna i en vanlig smartphone, som stöd till den nya referensarkitekturen, berättar Thomas Lundholm.
Något som forskarna på XPRES också tittat närmare på är människans roll i framtidens smarta fabriker. När datorerna en gång i tiden gjorde sitt intåg inom industrin trodde många att människan nästan helt skulle komma att ersättas av robotar. Men riktigt så långt är det ingen längre som tror att utvecklingen kommer att gå – åtminstone inte inom överskådlig framtid.
– Däremot kommer människan att få andra, mer kvalificerade arbetsuppgifter. De funktionella verkstäderna med en medarbetare vid en maskin kommer att försvinna. Framtidens smarta fabriker kommer istället att bemannas med experter och problemlösare som går runt och kontrollerar att produktionen fungerar som den ska, säger Magnus Lundgren, doktorand och forskare på XPRES.
Datasäkerhet en förutsättning
Men att personalbehovet kommer att minska råder inga tvivel om, vilket också kan vara lösningen på problemen med den demografiska utvecklingen. Både Sverige och Tyskland har en åldrande befolkning och går mot en brist på arbetskraft. Med ökad automatisering finns det möjlighet att klara produktionen med färre anställda.
– Digitaliseringen är ett överlevnadskrav för industrin – därav det stora intresset bland politikerna för produktivitetsökningar och utveckling av ny teknik, konstaterar Johan Stahre.
Men utvecklingen drivs också på av andra faktorer, som till exempel kortare produktlivscykler, krav på ökad kundanpassning och kostnadspress. En smart fabrik med självstyrande produktion ger både högre produktivitet och större flexibilitet – men till kostnader som är fullt jämförbara med massproduktion.
– En digitalisering av hela kedjan från produktidé till färdig produkt förkortar omställnings- och ledtiderna radikalt. Volvo Cars exempelvis har målet att reducera ”time to market” ned till 20 månader från ledningsbeslut till produktionsstart. Dessutom kan man i dag hantera betydligt fler modellvariationer än tidigare genom att man introducerat nya digitala lösningar, förklarar Thomas Stetter, divisionschef för Digital Factory i Norden och Polen på Siemens.
Samtidigt går det inte att bortse från att det också finns hinder på vägen, som till exempel säkerhetsriskerna. När fabriker och maskiner över hela jordklotet är uppkopplade via nätet ökar också riskerna för att informationen kommer i orätta händer.
– Trots det är det en utveckling som inte går att stoppa. Även om Industrie 4.0 handlar om evolution snarare än revolution och det säkert tar mer än 20 år innan processen är fullt genomförd överallt har vissa branscher, som till exempel bil- och flygindustrin, som är de mest konkurrensutsatta och globala, redan nått Industrie 3.8, fastslår Thomas Stetter.