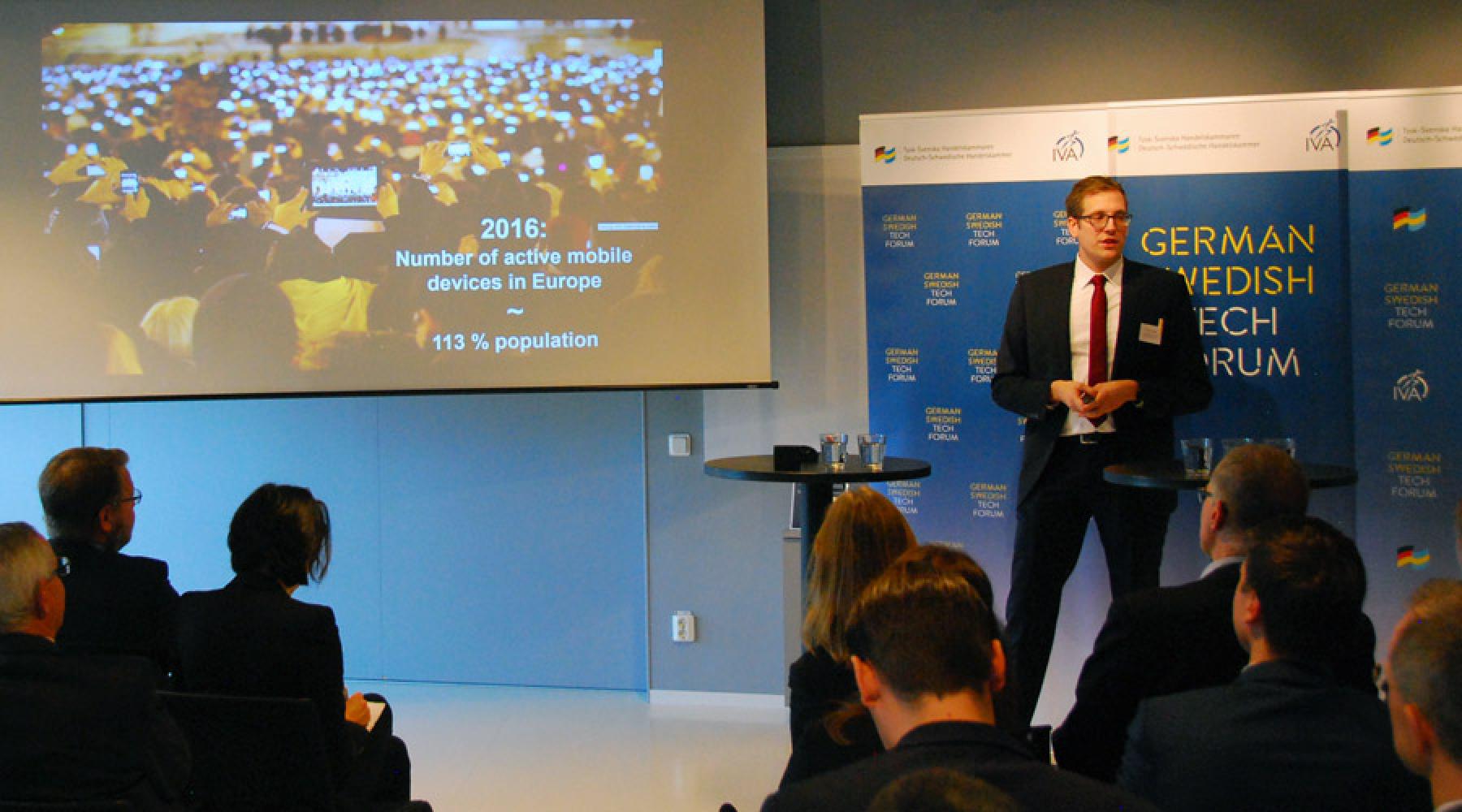
Durch Big Data lassen sich Prozesse verbessern und effektivieren, erklärte Florian Lindner.
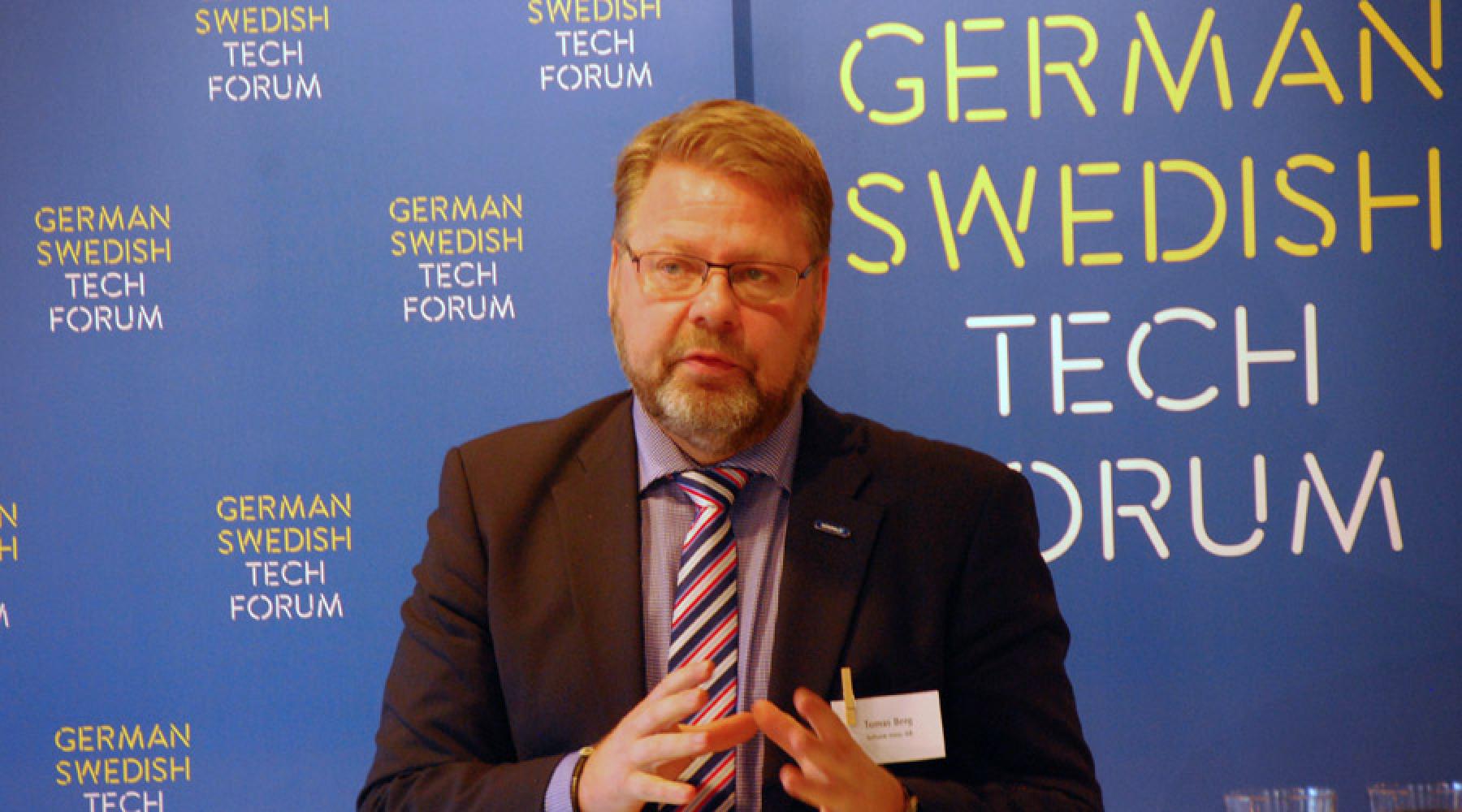
Aus der Digitalisierung ergibt sich ein völlig neues Geschäftsmodell, sagte Tomas Berg.
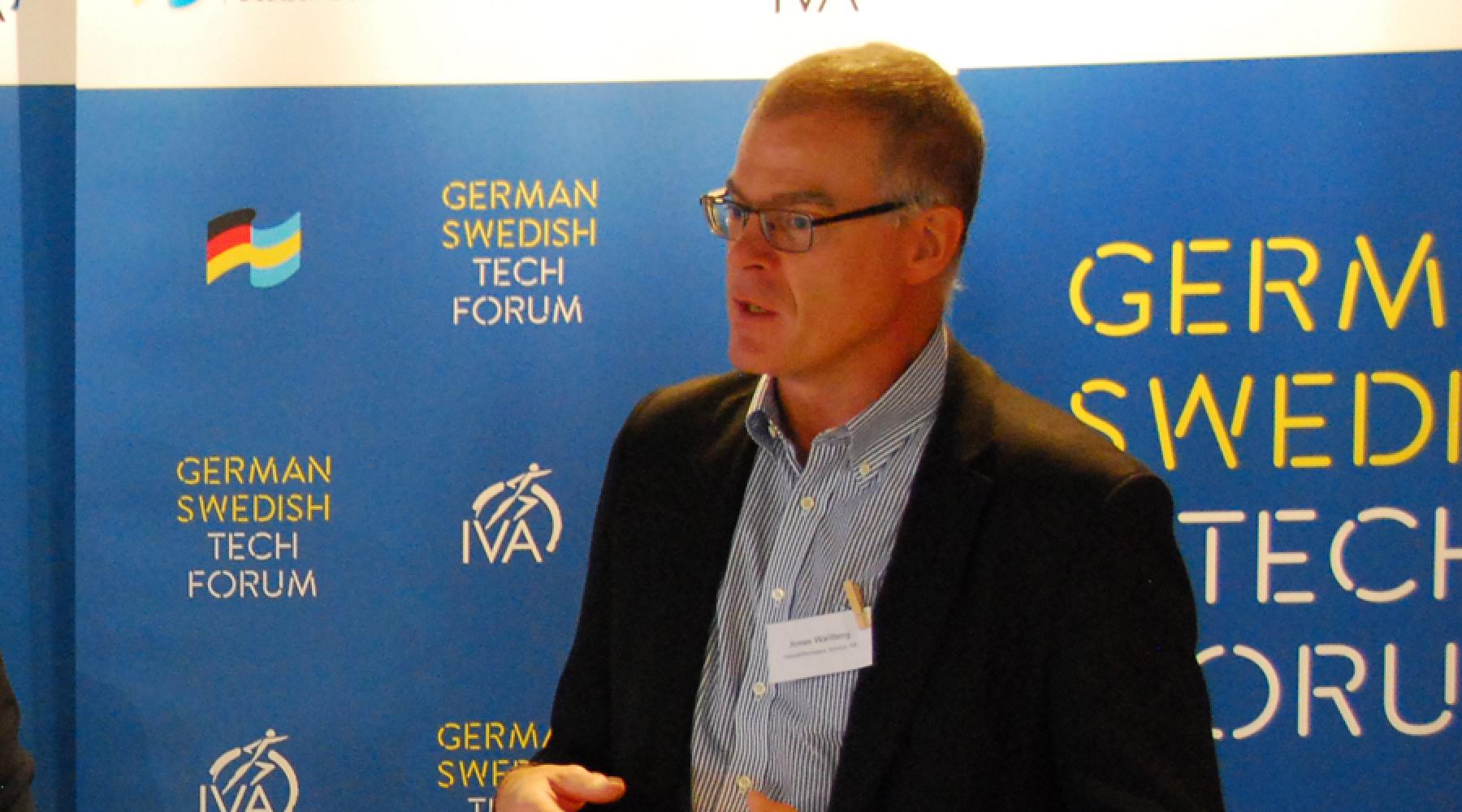
Die Unternehmen befinden sich momentan auf verschiedenen Levels, meinte Jonas Wallberg.

Jannik Henser stellte das neue deutsch-schwedische Testbed vor.
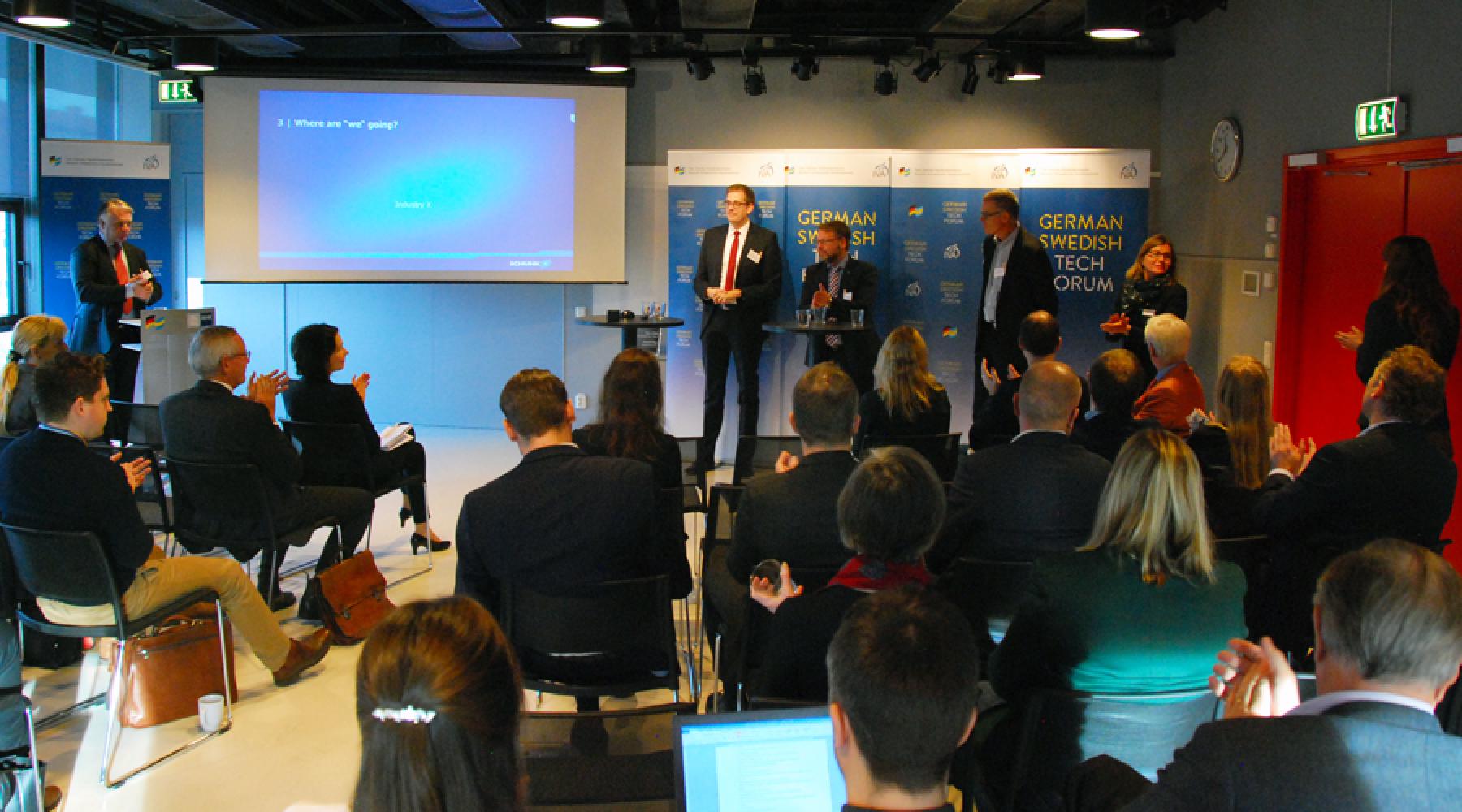
Das Seminar fand in der Deutsch-Schwedischen Handelskammer in Stockholm statt.
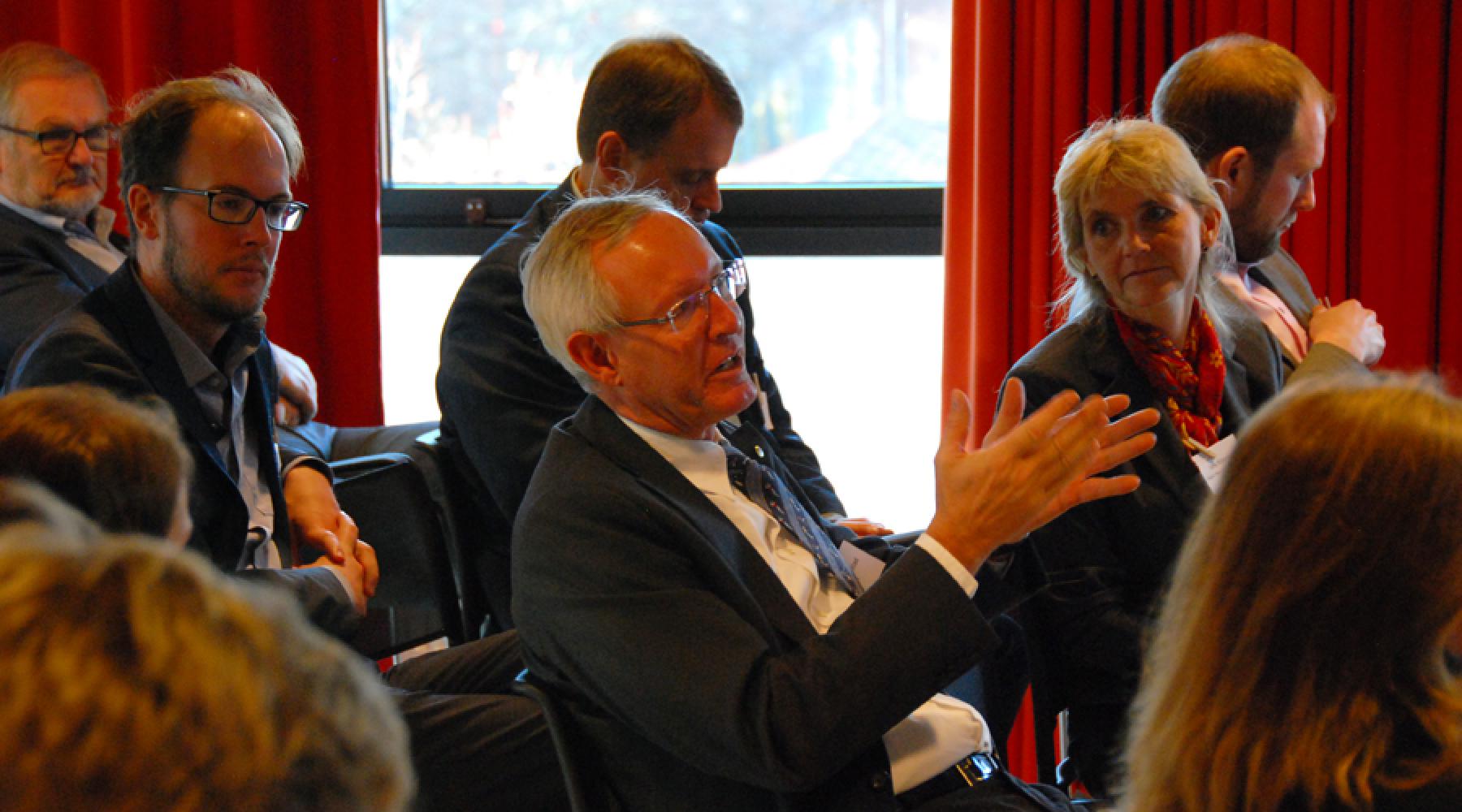
Die Seminarteilnehmer hatten zahlreiche Fragen an die Redner.
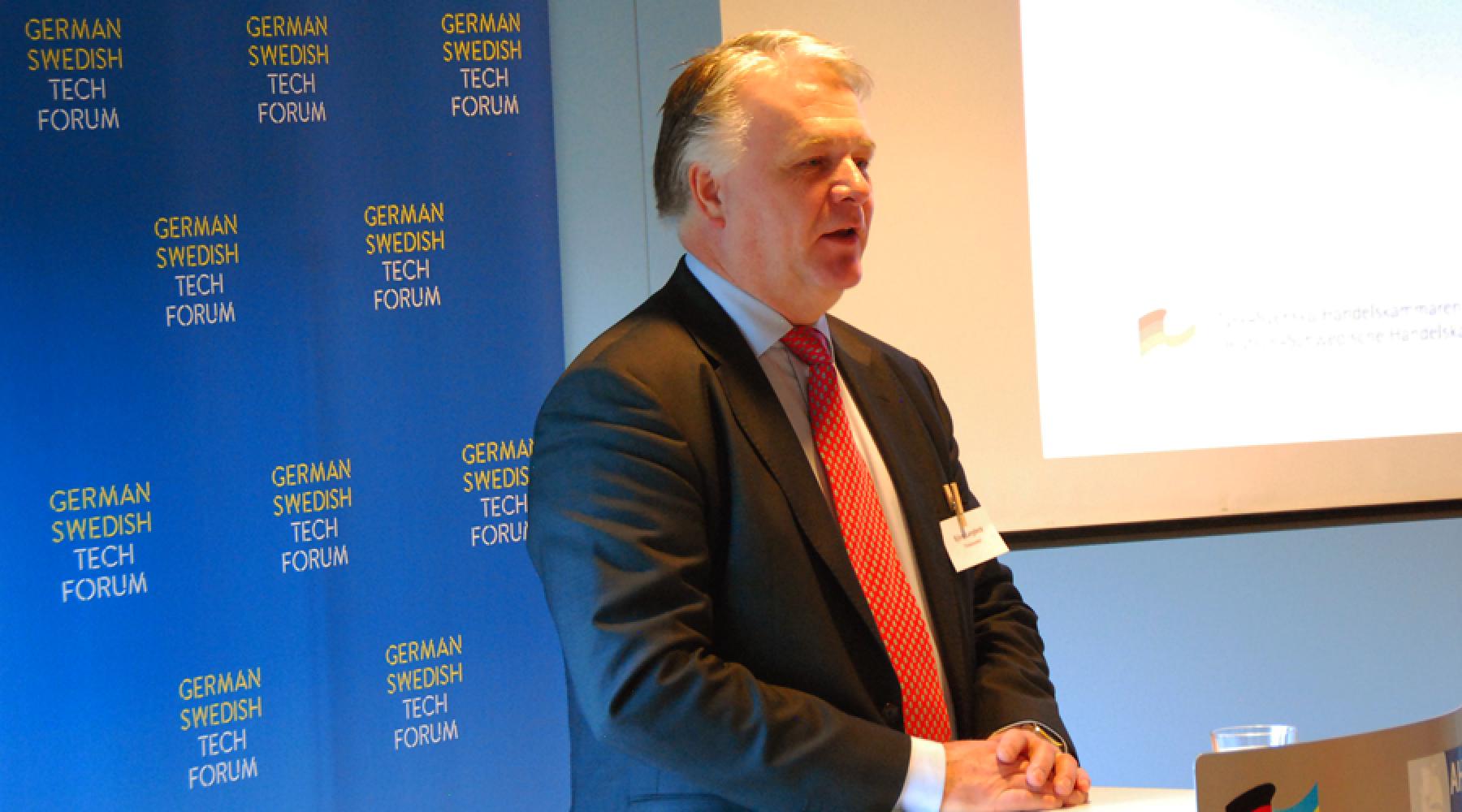
Moderator der Diskussion war Björn Langbeck, Industrieexperte bei Tillväxtverket.
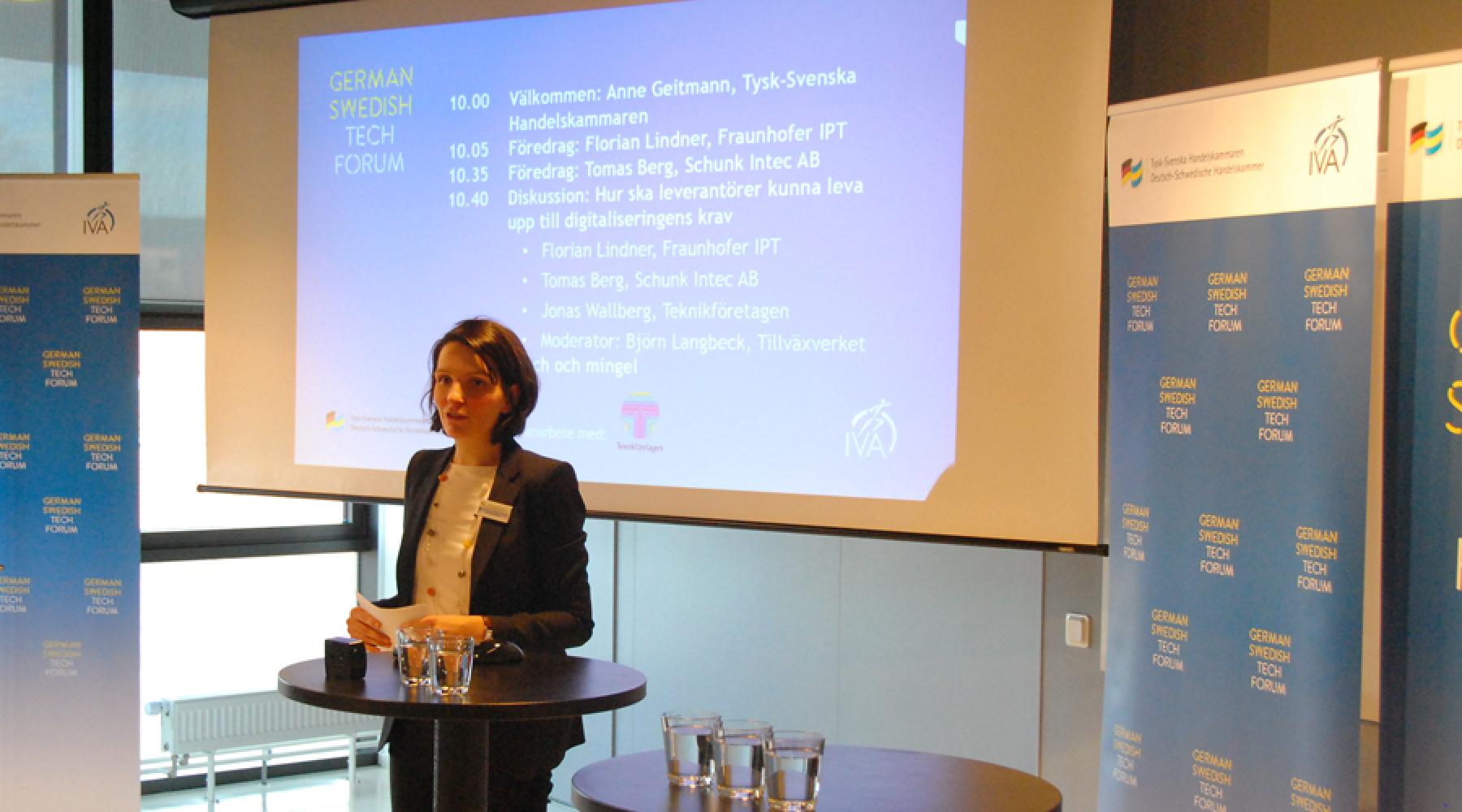
Anne Geitmann, Deutsch-Schwedische Handelskammer, begrüßte die Teilnehmer.
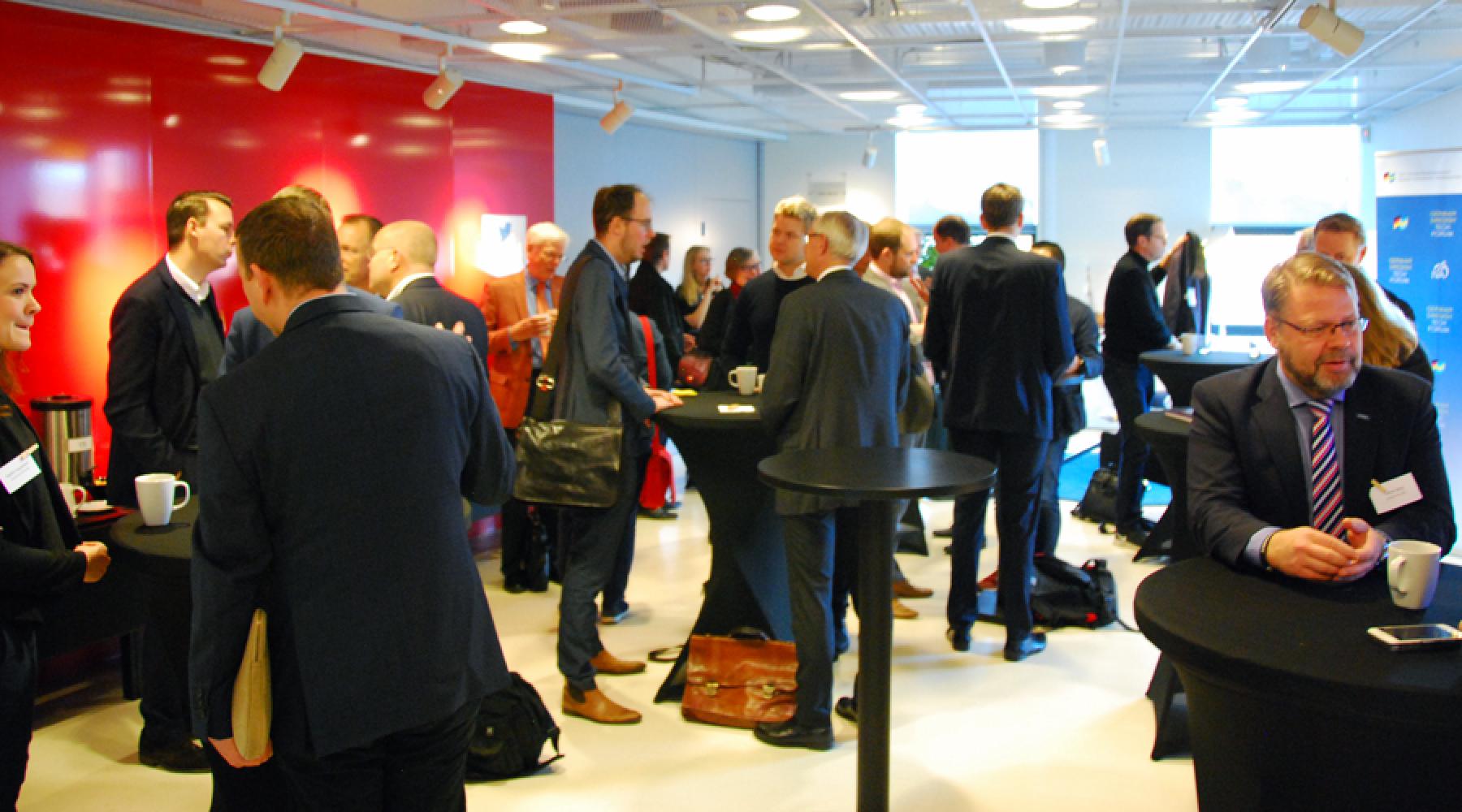
Vor und nach dem Seminar war Zeit für persönliche Gespräche.
Deutsch-schwedisches Testbed unterstützt Zulieferer bei der Digitalisierung
09.11.2017
Die Digitalisierung ist eher eine industrielle Evolution als eine Revolution. Als Zulieferer in der Industrie kann es eine gute Strategie sein, beim Digitalisieren Schritt für Schritt vorzugehen und auf eine enge Zusammenarbeit mit Kunden, Branchenkollegen und über Ländergrenzen hinweg zu setzen, zum Beispiel durch eine Beteiligung am neu eingerichteten deutsch-schwedischen Testbed. Dies wurde beim German Swedish Tech Forum-Seminar in der Deutsch-Schwedischen Handelskammer am vergangenen Dienstag deutlich.
Die eigenen Produktionsabläufe, Systeme und Produkte zu digitalisieren und damit für die Zukunft fit zu machen, ist eine der größten Herausforderungen, vor denen Industrieunternehmen heute stehen. Für mittelständische Unternehmen, die andere Firmen mit Komponenten beliefern, ist es jedoch nicht ganz einfach, zu wissen, wie man dabei vorgehen soll: Wie erfüllt man die Anforderungen der Kunden, besonders wenn unterschiedliche Kunden unterschiedliche Vorstellungen und Vorgehensweisen haben? Welche Systeme und Prozesse werden für eine digitale Produktion benötigt? Und wo erhält man Unterstützung, um die notwendigen Veränderungen in die Tat umsetzen zu können?
Um den Unternehmen zu helfen, einige Antworten auf diese Fragen zu finden, hatten die Deutsch-Schwedische Handelskammer und die Königlich Schwedische Akademie der Ingenieurwissenschaften (IVA) in Zusammenarbeit mit dem Industrieverband Teknikföretagen zu einem Seminar im Rahmen der deutsch-schwedischen Innovationsplattform German Swedish Tech Forum eingeladen. Dabei beschrieb Florian Lindner, Gruppenleiter in der Abteilung für Produktionsqualität am Fraunhofer-Institut für Produktionstechnologie (IPT) in Aachen, was man alles erreichen kann, wenn man das volle Potenzial der Daten nutzt, die digitalisierte Maschinen und Produkte erzeugen.
„Von allen Daten, die heute in der Industrie generiert werden, sind 90 Prozent derzeit unstrukturiert und auf mehrere Systeme verteilt. 70 Prozent der Daten werden überhaupt nicht genutzt und für 96 Prozent gibt es weiteres Potenzial. Durch den zielgerichteten Einsatz von Big Data lassen sich Prozesse jedoch erheblich verbessern und effektivieren – das haben zahlreiche Großkonzerne bereits in der Praxis bewiesen. Insgesamt gibt es vier Schritte bei der Datenanalyse: Zunächst einmal kann man Informationen darüber generieren, was genau in der Produktion abläuft. Dann lassen sich Muster erkennen, warum gewisse Dinge passieren. Im nächsten Schritt kann man Prognosen erstellen, was in der Zukunft geschehen wird, und final wird es möglich sein, die Systeme mithilfe von Daten aktiv zu kontrollieren und einzugreifen, noch bevor Fehler oder Störungen auftreten. Dabei bewegt man sich vom bloßen Sammeln von Informationen hin zur Prozessoptimierung.“
Neues Geschäftsmodell dank integrierter Systeme
Big Data-Lösungen einzuführen, die derartige Ergebnisse liefern, ist eine große Herausforderung für Zulieferer, da es Ressourcen und technische Expertise erfordert. Aber es geht nicht nur darum, sagte Tomas Berg, General Manager bei Schunk Intec in Schweden, einer Tochtergesellschaft der Schunk GmbH & Co. KG, Weltmarktführer für Greifsysteme und Spanntechnik:
„Die größte Herausforderung liegt nicht in der Technik, sondern in der Denkweise und Einstellung. Künftig werden alle Systeme miteinander vernetzt sein, nicht nur innerhalb der eigenen Firma, sondern auch mit den Systemen der Kunden und Zulieferer. Daraus ergibt sich ein völlig neues Geschäftsmodell. Der Kunde wird immer größeren Einfluss darauf bekommen, wie die Produkte aussehen, welche Funktionen sie haben und wie sie bestellt werden können. Diese Entwicklung wird sich nur immer weiter verstärken.“
Es geht jedoch nicht überall gleich schnell voran. Die Diskussionsteilnehmer waren sich darin einig, dass die Digitalisierung nach und nach sämtliche Branchen erfassen wird, aber dass die Unterschiede in der Geschwindigkeit groß sind.
„Die Unternehmen befinden sich momentan auf verschiedenen Levels. Auch unter den global agierenden Großkonzernen gibt es immer noch eine ganze Reihe, die in Sachen Digitalisierung noch nicht so weit vorangekommen sind. Zum Beispiel haben viele Großkonzerne noch kein EDI [Electronic Data Interchange, Elektronischer Datenaustausch, Anm. d. Red.] eingeführt, was den Informationsaustausch mit den Zulieferern erheblich vereinfachen würde. Im Prinzip nutzt derzeit nur die Automobilindustrie EDI. Sie ist hier Vorreiter, sowohl in Schweden als auch in Deutschland“, sagte Jonas Wallberg, Digitalisierungsverantwortlicher bei Teknikföretagen.
Zusammenarbeit zwischen Forschungsinstituten und Unternehmen
Eine konkrete Initiative, um die Digitalisierung mittelständischer Zulieferbetriebe voranzubringen, ist das „Deutsch-Schwedische Testbed für Industrie 4.0“ (Swedish-German Testbed for Smart Production), das im Zusammenhang mit der Eröffnung des German Swedish Tech Forum und der Unterzeichnung der Erklärung über eine Zusammenarbeit zwischen der deutschen und der schwedischen Regierung im Januar dieses Jahres ins Leben gerufen wurde. Mehrere deutsche und schwedische Forschungsinstitute und Unternehmen arbeiten im Rahmen des Testbeds zusammen. So soll die fachliche Expertise in beiden Ländern zusammengeführt und der Austausch zu technischen Lösungen und Erfahrungen für die digitalisierte Fertigung anspruchsvoller Bauteile für die Automobilindustrie verstärkt werden.
„Mit dem Testbed bekommen deutsche und schwedische Unternehmen eine sehr gute Plattform für die Arbeit an richtigen praktischen Herausforderungen und die Erprobung möglicher digitaler Lösungen“, sagte Florian Lindner.
„Wir planen, im Rahmen des Testbeds sowohl an der horizontalen als auch der vertikalen Integration von digitalen Lösungen sowie an der digitalen Infrastruktur zu arbeiten. Wir wollen beispielsweise sogenannte digitale Zwillinge von Bauteilen erstellen und Daten aus dem Fertigungsprozess integrieren, um Eigenschaften und Veränderungen über einen bestimmten Zeitraum hinweg simulieren zu können. Damit dies gelingt, brauchen wir sowohl reale Daten als auch Ingenieure mit Fachkenntnissen aus der Produktion“, erklärte Jannik Henser, Geschäftsführer des Powertrain Manufacturing for Heavy Vehicles Application Lab (PMH), einer Kooperation zwischen der Königlich Technischen Hochschule (KTH) in Stockholm, der Fraunhofer-Gesellschaft und des schwedischen Netzwerks für Forschung und Technik RISE.
Realisiert wird das Testbed im ersten Schritt an den Standorten Stockholm (PMH), Aachen (IPT) und Chemnitz (am Fraunhofer-Institut für Werkzeugmaschinen und Umformtechnik IWU). Später sollen weitere Partner angeschlossen werden. Momentan bereitet man die ersten konkreten Tests vor und die Branche ist eingeladen, sich aktiv in die Arbeit einzubringen:
„Interessierte Unternehmen, besonders mittelständische Zulieferer, sind herzlich willkommen, sich mit ihren Ideen und Lösungen an der Initiative zu beteiligen. Zusammen können wir eine kritische Masse bilden und die Standards der Zukunft entwickeln“, schloss Jannik Henser ab.